How we built
our OE 32 Otium
The chairman of the OE Club, Biörn Johansson, and his wife Majbritt began building their OE 32 Otium in the autumn of 1980. It was launched at midsummer in 1984. In between, lay a time of continuous work with the construction.
Biörn has documented his building work step by step, interspersed with many photographs. An assortment of these photographs are shown below.
To enlarge the photographs, click on the small images. To close the window containing the large photograph, click anywhere on the picture.
Björn and Majbritt had already built and owned two boats. The first one was a twin cabin, Scandinavian double ender made of oak. Boat number two was a Laurin Scandinavian double ender in beautiful mahogany which was built around 1970 with some modifications of the original Laurin design. She was around 9 metres (29ft 6in) in length and had a beam of 2,5 metre (8ft 1in). She remained in the couples hands for 11 years.
Around 1980, Biörn began to understand that as well as himself and his wife, the boat was getting on in years. When the old man is getting long in the tooth there is not much you can do about it. But an ageing mahogany boat should of course be replaced with a new one reasoned the pair. After many discussions and a lot of hesitation they decided to take on a third boat building project. That would be an OE 32.
In the autumn of 1980 they began the construction. The mould and the materials for building the hull, as well as skilful craftsman were already at Sundsörs ship yard in Oxelösund. There, the promoters of the OE-boats had established a small area with a qualified and cost effective organisation for self building under expert guidance.
In the beginning, the construction proceeded quickly. A bright, new shiny hull was already completed after a couple of weeks.
First a gel coat was sprayed on the inside of the two well waxed moulds, one for the starboard half of the hull and the other for the port side. |
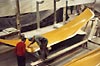 |
After that, slices of fibreglass mats (450 g/sqm), cut out by the template that the ship yard had supplied, were applied to the mould. The mats were carefully applied to the gel-coated form and later, polyester plastic was rolled on by hand. |
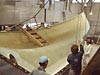 |
The next step involved the application of the sandwich filling of divinycell. This material is laid out on the damp polyester and is compressed until the polyester hardens. Afterwards, an additional layer of fibreglass and polyester is added. The result is a double laminated hull with divinycell as the filling material between the outer and inner layers. The hull is thus both strong and insulated, which prevents condensation from forming. After that, it is time to apply the next layer of fibreglass and polyester to the inside of the soon-to-be hull. |
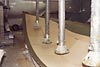
|
The deck, rudder and the hatch are manufactured separately.
|
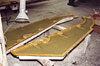 |
They were sweaty days, recalls Biörn but it was also a lot of fun. The atmosphere was rough but hearty. After the long working days with breathing equipment and altogether far too warm safety clothes one felt really tired. One leaned their stiff pants against the wall, and had no problems sleeping at night.
|
When the hull halves had hardened they were carefully loosened from the moulds and pushed together. They were temporarily screwed together with bolts around the edge of the form. It was beginning to look like a boat! |
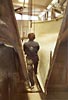 |
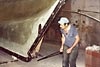 |
The next working stage consisted of filling the keelson with heavy lead pieces and then pour molten lead over and between the lead pieces. Earlier, I had built a transverse floor plate in the keelson in front of the engine room to prevent the molten lead running into the engine room, where the fuel tank was also later going to be installed. The lead was melted in a large witchs cauldron and poured out with a ladle. To prevent the fibreglass in the keelson from melting, the outside of the hull was constantly flushed with cold water |
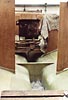 |
Now it was time to fit in and to fibreglass the bulkheads to the hull. |
 |
Afterwards, the deck could be attached like a lid. It was joined with bolts and bonded to the hull with fibreglass resin to make it strong and tight. Finally, the engine was installed (a Volvo Penta MD 11). |
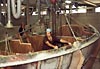 |
Here are the two halves of the hull fibreglassed together. |
 |
All of this had been completed in only two weeks and the result was something that definitely resembled a boat. The day came when the creation was placed on to a trailer in order to transport it home to the front lawn of Biörn and Maj-Britts place in Tyresö. There the construction resumed and it seemed like it was going to take a long time. Almost three years, strictly speaking! |
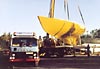 |
Once she arrived at the garden, she was set on chocks and covered with tarpaulin before the winter set in. Because of the cold in winter the work could only continue once spring broke through and then, only with the help of a cabin heater.
The work began with the manufacture and fibreglassing of some additional transverse floor plates in the keelson. It demanded some brainwork to consider the future placement of the batteries. It would be annoying if they didnt fit between the floor plates. Afterwards we assembled the mast foot.
Biörn got on with the carpentry work. An almost discouraging number of finished sawn teak pieces, screws and nuts were collected from the shipyard. Now it was a matter of fitting them together in the correct order. |
Biörn started with the toe rail (or gunwale), the teak deck and the teak areas in the cockpit. |
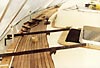 |
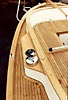 |
He continued with all of the countless details of the interior fixtures and fittings. At that time Sören Oldebäcks first-rate building manua for the OE 32 wasnt available. However the equivalent book for the OE 36 was available and Biörn was therefore able to use that one. The work was made easier because the interior modules for the OE 32 and the OE 36 were largely the same. On the other hand, the hulls of these two boats were very different. Therefore it was a matter of both thinking as well as precision to make the pieces to fit nicely. |
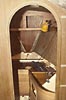
Working
in the fore cabin |
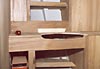
Working
in the toilet space |
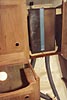
The septic tank |
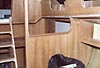
The cabin |
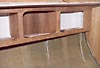
The cupboards and bookshelves |
|
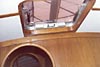
The skylight
in the fore cabin
is finished |
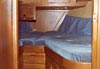
The fore cabin
is complete |
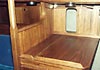
The navigation area is ready |
During this time, Biörn and Majbritt also travelled to London to buy equipment and fittings for the boat.
Biörn worked as a full time fire chief, but in shifts. He had no more spare time than other workers and practically all of his free time was spent on the boat. Many who began to enthusiastically build a new boat ran out of steam at this stage. That is to say, it wasnt always just a case of being a handyman. Devotion, resolution and stamina were just as important prerequisites in order to gradually complete the boat project.
The one who resolutely keeps going and never gives up can rejoice in the fact that the work becomes more enjoyable as one comes closer to the goal. It is so satisfying to finally put on the satin varnish after figuring out all the pieces of joinery
Biörn and Majbritt dont know exactly how many hours the building of the boat took but they thought that it had taken a minimum of approximately 5,000 hours! Think about that all of his spare time over three to four years of patiently working on the construction! In truth, it is an impressive achievement!
The almost completed boat, was, after three years, transported down to the boat clubs harbour at Tyresö, where the mast and rigging also came. Once the mast was on, the boat was launched in the midsummer of 1984 almost four years after the project had started at the shipyard in Oxelösund. The result was a really first-class boat of excellent quality with a high finish. It was also at that time, a relatively large boat. A ship stated Biörn when he compared it with his earlier boats.
|